Although hydrogen fuel cell vehicles (FCEVs) have been around since the 1960s, they have only recently emerged as a potential solution to decarbonizing heavy transportation. Nikola Motors just announced it has raised $1 billion in funding for hydrogen vehicle technology, adding some key new partners including CNHI and Bosch. Earlier this year, the company also launched an aggressive roadmap for 700 gas stations across the U.S. and secured an 800-vehicle partnership with Anheuser-Busch to help decarbonize its freight fleet.
What makes FCEVs a good option for decarbonizing heavy transportation? Let’s examine the similarities, advantages, and challenges of FCEVs compared to traditional internal combustion trucks.
Hydrogen fuel pumps: such as diesel and gasoline
One benefit of FCEVs is that hydrogen uses a fueling infrastructure similar to traditional trucks. This means that FCEVs can be refueled at truck stops located across the country and the refueling experience will be similar. The truck can be filled with hydrogen in less than 15 minutes, and the process of fueling an FCEV is similar to that of fueling a diesel truck; Hydrogen gas is pumped into the vehicle’s tank using a gas pump and nozzle similar to a conventional diesel pump.

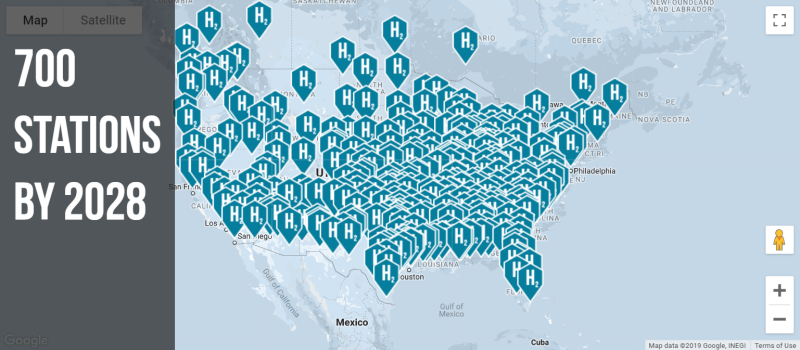
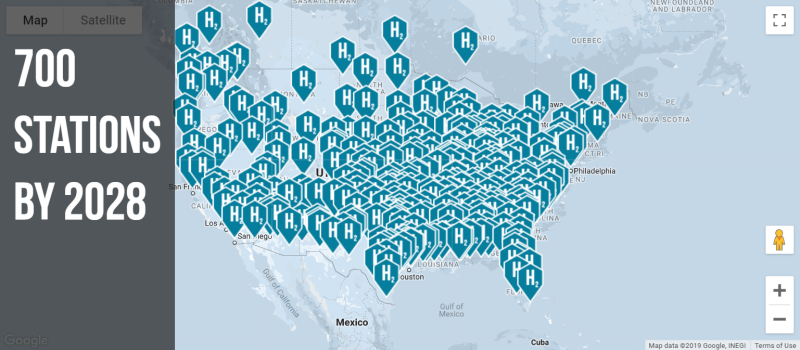
Source: Nikola Motors
Higher energy density
Another advantage is the energy density of hydrogen. Diesel has an energy density of 45.5 megajoules per kilogram (MJ/kg), which is slightly lower than gasoline, which has an energy density of 45.8 MJ/kg. In contrast, hydrogen has an energy density of about 120 MJ/kg, nearly three times that of diesel or gasoline. In electrical terms, hydrogen’s energy density equals 33.6 kWh of usable energy per kg, versus diesel which only carries around 12-14 kWh per kg.
What this really means is that 1 kg of hydrogen, used in a fuel cell to power an electric motor, contains roughly the same energy as a gallon of diesel. With that in mind, Nikola claims its vehicles can get the equivalent of between 12 and 15 mpg, which is well above the national average for a diesel truck, which is about 6.4 mpg.
Much less heat loss
Electric propulsion engines are also more efficient than internal combustion engines. With an internal combustion engine, approximately 50% of the energy generated is converted into heat; But electric transmission systems lose only 10% of their energy to heating. This difference in efficiency shows how much consumers lose with less efficient internal combustion engines.
Get cheaper
Price is another attractive attribute of hydrogen. Diesel prices are currently approaching $3.00 per gallon, and with the recent reduction in oil production in Saudi Arabia, it is reasonable to expect further increases in diesel prices. But on the hydrogen front, recent analysis from Bloomberg New Energy Finance suggests that the price of producing one kilogram of hydrogen could reach $1.40 per kilogram within a decade.



Source: Nikola Motors
Fuel cell is lighter than batteries, longer range
When it comes to heavy transport, weight matters. FCEVs offer the same high torque that comes with battery electric vehicles, but with less weight. Examples include the estimated weight difference between the Lion 8 electric battery and the Nikola One hydrogen fuel cell; The Lion 8 has a 480 kWh battery with a range of 250 miles, which equates to about 2-5 tons. The Nikola One, which has a range of about 500-750 miles, is estimated to have a 250 kWh battery, which would likely weigh about 2.5-3 tons.
With these factors in mind, there is a clear path for hydrogen to become a low-carbon, low-cost, low-weight alternative fuel for heavy trucks.
However, FCEV trucks are not without challenges.
There is not enough “green hydrogen” production. Until now
Although hydrogen gas has no color or smell, to support the decarbonization of heavy transportation, we’ll need green hydrogen, and lots of it. Green hydrogen, also called renewable hydrogen, is hydrogen made using only renewable energy, usually through the electrolysis process. Water electrolysis uses electricity to separate water into gaseous hydrogen (H2) and oxygen (O2), converting electrical energy to chemical energy. Questions remain about how quickly green hydrogen production can scale up; The capacity to manufacture electrolyzers has begun to increase significantly.

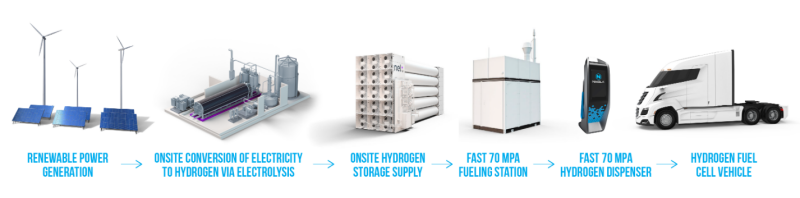
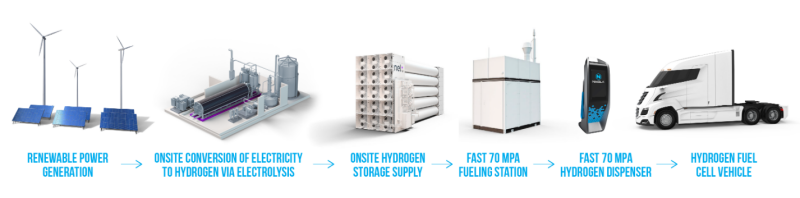
Source: Nikola Motors
Transportation and storage. how?
The main challenges related to hydrogen are transportation and storage. Hydrogen is produced in gaseous form and must be stored under pressure or liquefied directly. Both processes require additional energy, which may or may not be from renewable sources.
There are emerging methods that use chemical bonds (commonly referred to as liquid organic hydrogen carriers (LOHCs)) or ammonia to transfer hydrogen in a steady state. These methods do not require compression or cryogenic liquefaction, and therefore require less energy to transport and store hydrogen. However, this technology is still in a relatively early stage of development and is not ready for widespread use.
Producing hydrogen locally? Use existing gas pipelines?
Another solution to transportation and storage challenges is to focus on local production. Nikola has partnered with Nel and Bosch to provide a network of local hydrogen production plants that use renewable energy sources and electrolyzers, thus cutting the logistics chain of traditional diesel and gasoline supplies.
In the future, we can also use natural gas infrastructure to transport hydrogen, reducing the need for large infrastructure development. This could also provide a way to supply hydrogen from central production centers rather than local buildings.
Diesel outperforms hydrogen in range
Another disadvantage of hydrogen is range. According to Nikola, the range of a fuel cell truck is between 500 and 750 miles, depending on payload and terrain; Toyota Kenworth FCEV trucks have a range of about 300 miles. This pales in comparison to diesel trucks, which can travel more than 1,000 miles without refueling. However, since drivers are limited to 500 miles per day, this factor may not cause a significant disruption to standard practices.
Clean fuel policies and investments
Although there are challenges, the time is right for hydrogen, and here’s why:
We are seeing increased regulatory pressure and demand in the industry. The European Union has committed to eliminating gasoline and diesel vehicles by 2030. On the other hand, clean fuel standards and associated investments in California and Canada are creating the political basis for change. Hyundai plans to produce up to 700,000 FCEVs annually by 2030, and Japan aims to produce 800,000 FCEVs by 2030. With technology costs expected to reach break-even with diesel trucks in many markets, there is significant momentum and investment in hydrogen.
The more projects that increasingly use fuel cell technologies, the greater the possibility of reducing costs and investing in the technology. China’s commitment to put 1 million fuel cell vehicles on the road by 2030 (with a $7.6 billion investment in heavy trucking) offers huge potential for significant progress on the efficiency and cost points of fuel cell vehicles.
Hydrogen has seen a false dawn before, but this low-carbon alternative is being pushed by some of the biggest companies on the planet across multiple sectors. Toyota Kenworth has a strong track record of developing trucks using fuel cell technology, and in 2019 added 10 T680 trucks for use at the Port of Los Angeles and throughout Southern California. Shell has recently invested heavily in large-scale hydrogen electrolyzers, which provide a carbon-neutral option for hydrogen production. Earlier this month, Cummins acquired market-leading electrolyzer and fuel cell manufacturer Hydrogenics for $290 million. These are all signs of serious commitment by industry leaders to move into hydrogen and fuel cells.
The Rocky Mountain Institute (RMI) is identifying opportunities for green hydrogen to accelerate decarbonization in sectors that have struggled to make progress, and we are only now beginning to see the role and place this technology can play in decarbonizing the shipping sector. Watch a panel discussion on hydrogen in trucking, hosted by the North American Council for Freight Efficiency (NACFE).
***
Patrick Molloy is a senior fellow in industrial and heavy transportation at the Rocky Mountain Institute
This article is published with permission. Copyright 2019, Rocky Mountain Institute